The plastic used in commercial PP and PET straps comes from either polypropylene (PP) or polyester (PET). While a higher quality PP is typically made from virgin resin, PET is manufactured with up to 100% recycled material consisting of bottle flake or reprocessed pellets.PP and PET straps are produced by extrusion through either one of two processes: multi-strand or sheet. The strands are individually extruded through a multi-opening die, stretched, annealed and then cooled.EAM-Mosca manufactures PET strapping using up to 100% recycled material, including recycled bottle flake and reprocessed PET pellets. This makes PET a more sustainable packaging choice with post-use recyclability.
The temperature used in the
extrusion line for PET straps is an important factor with respect to the brittleness of the material. The brittleness is largely controlled by the temperature range in which the third stretching stage takes place.In order to control brittleness, the temperature range in which the third stretching stage is conducted should be kept in the lower 200deg F. area unless the customer is concerned with brittleness or the tensile strength of the material cannot be increased beyond this point.
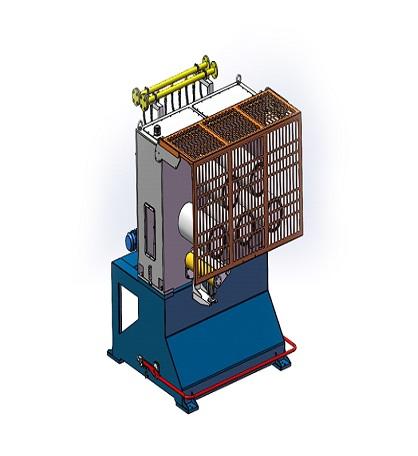
The brittleness of the material can be improved by surface treating it in order to provide it with an outer layer of a suitably amorphous character. This is accomplished by exposing the material to heated rolls or other means that raise its surface temperature. The surface may then be chilled using chill rolls or other means that cool the material to a temperature in the lower 0deg F. region.PET strapping (also known as polyester or polythene terephthalate) is a durable and safer alternative to steel straps. It is also able to retain its tension and stretch recovery properties for a long period of time, making it more resistant to shocks and impacts.
The pressure used in the extrusion line for PET straps depends on the type of PET material and the desired tensile strength. The straps may be extruded in a sheet manner or individually stranded.In the case of a sheet, the material is extruded to produce a consistent strap profile from one strap to the next. However, individual strand extrusion can provide more flexibility in the production process because it allows a more variable cross-sectional profile.It is also possible to improve the weldability of the strap by surface treating it with a suitable amorphous layer. The amorphous surface layer can be produced using a coextrusion technique and the benefits of surface treatment can be obtained without a significant reduction in the overall strap strength.
The cooling process is an important aspect of extrusion. It helps maintain the material's shape and prevents the sheet from deforming while it travels through the machine.In addition to temperature, extruders use other factors to determine cooling time. These include polymer's thermal conductivity, specific heat and specific weight.Extruders also need to control the melt temperature and screw geometry to provide high-quality straps. This is important for pet food processors because it allows them to produce the high-quality, high-strength products needed to compete in the market.